Understanding NPN and PNP Sensors: A B2B Guide for Industrial Automation
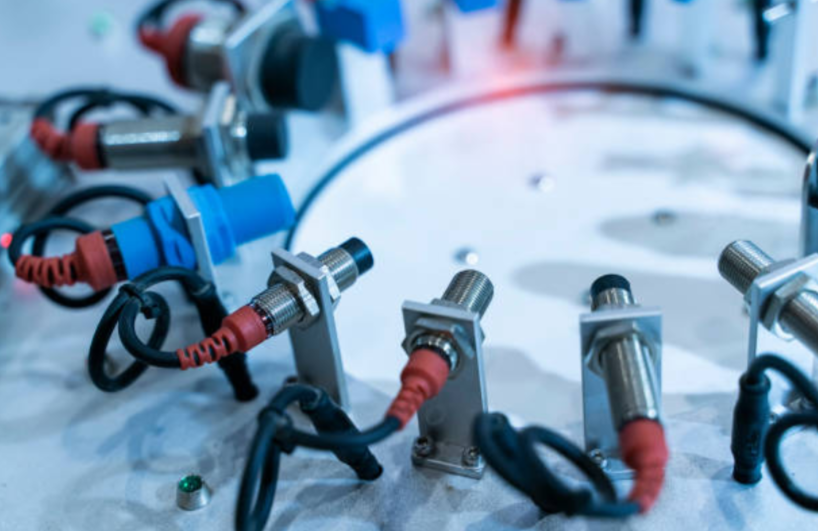
In industrial automation, proximity sensors keep machines running smoothly, safely, and with high accuracy. Two of the most widely used types are the NPN and PNP sensors, and each one has its own electrical behavior. For B2B firms that design machines, automate processes, or build control systems, picking the right sensor matters a lot-it can make or break compatibility and overall system performance.
This guide breaks down the basics of NPN and PNP sensors, points out how they differ, and lists the things businesses should think about before adding them to any setup. It also mentions reliable suppliers like Omchele, which stocks a broad range of sturdy proximity sensors for nearly any automation task.
Check out Omchele’s https://www.omchele.com/es/proximity-sensors/ .
What Are NPN and PNP Sensors?
NPN and PNP sensors are both three-wire DC proximity sensors that detect objects without needing to touch them. When an object enters their sensing zone, they send out a switching signal that shows the presence of that object, making them ideal for linking with PLCs or other control units.
Both types of sensors do the same job, but they behave differently when it comes to how they send out power.
- An NPN sensor, sometimes called a sinking sensor, pulls the load down to ground when it is turned on. That means current moves from the power supply, through the load, and finally through the sensor to the negative side.
- A PNP sensor, in contrast, is a sourcing sensor that pushes the load up to the positive voltage when it activates. Here, current flows from the positive line, through the sensor, and into the load.
Even though both sensors can detect the same objects, each one works better with certain control systems. Picking the wrong type may cause the entire system to fail or force you to spend extra money on rewiring.
Core Differences and How They Affect System Design
From a technical standpoint, understanding the output behavior of these sensors is essential. When the sensor detects an object, the NPN sensor pulls its output line to ground (0V), whereas the PNP sensor pushes the output line to a positive voltage level (typically 24V DC).
In most European and North American B2B systems, engineers lean toward PNP sensors because popular PLC brands expect a positive input. On the other hand, NPN sensors show up more often in Asian-made gear, particularly small or modular machines.
Wiring them is straightforward since color codes stay consistent: brown for positive (V+), blue for ground (0V), and black for signal. Still, that black wire does completely different jobs depending on whether the sensor is PNP or NPN.
Because of this, anyone building panels, integrating systems, or making original equipment needs to check which input type the control system uses before picking a sensor.
Industrial Applications of NPN and PNP Sensors
NPN and PNP sensors show up in just about every industrial job that needs quick, reliable feedback. You’ll find these devices helping with:
- Position detection on assembly and packing lines, making sure everything lines up perfectly
- Object counting on conveyor belts in warehouses, so inventory numbers stay accurate
- Limit switching in CNC mills and other machines, knowing when a tool has hit its travel end
- Feedback control in robotic arms, guiding them to grab, move, or release parts with precision
- Safety verification in high-speed sorters, double-checking that no one gets too close to dangerous areas
- Presence sensing in pick-and-place and bottling setups, confirming every bottle or jar is exactly where it should be
In every case, the sensor sends a clear signal to the controllers that boss the motors, lights, and alarms. If the signal is shaky, entire lines can stall or worse, raise safety hazards. Because production plants often run nonstop and mistakes cost money, reliability, durability, and electrical fit matter a lot.
That’s why partners choose brands they can trust, like Omchele. Their NPN and PNP units are built for harsh floors, greasy palms, and hot panels. Check out Omchele’s full line of proximity sensors to find the perfect match for your automation project.
Key Considerations for B2B Sensor Selection
Picking the right NPN or PNP sensor goes well beyond checking voltage or plug style. You’re designing a system that has to perform flawlessly in tough factory conditions, so keep these real-world tips in mind.
- PLC compatibility: First, find out if your controller uses sourcing (PNP) or sinking (NPN) signals. That single detail tells you which sensor to buy.
- System standardization: Big companies running multiple plants save time and money by sticking to one sensor type—PNP usually wins.
- Mounting space and sensor shape: M12, M18, and rectangular options let you slide the sensor into almost any machine layout without extra machining.
- Detection range: Pair the sensing distance with the job: short range for cramped areas, longer reach for conveyor or lift applications.
- Environmental resistance: Dust, oil, and water happen on the shop floor; IP67 sensors keep internal parts dry and working.
- Response speed: Super-fast lines or robotic arms need sensors that flip on and off in microseconds-make sure the spec sheet shows the speed you require.
- Connector type: Decide early on whether quick-disconnect plugs or hardwired cables suit your crew; the right choice cuts troubleshooting time in half.
By pausing to consider these points, B2B companies can skip the headaches of delays, re-wiring, or mismatched systems that slow down production and quality checks.
See Also: The Future of Biometric Technology: Security and Privacy
Evolving Trends in Sensor Technology and Integration
Today`s factories are smarter, and even low-tech sensors like NPN and PNP types have upped their game. While they still switch on and off the same way, engineers now see handy features such as:
- Short-circuit and overload protection, boosting safety and cutting the amount of downtime
- LED indicators, which show system status at a glance, during both setup and regular runs
- Extended temperature ranges, letting sensors work steadily in heat, cold, or shock
- IO-Link support, so teams can pull settings, run diagnostics, and gather maintenance clues through one line
For B2B clients trying to outfit plants that last, these extras deliver real long-term savings. Predictive alerts from smart sensors, for instance, slash surprise shutdowns, and IO-Link`s uniform plug cuts integration fuss across different brands.
Omchele stays ahead by rolling out sensors that handle routine spotting yet meet the latest comm, and safety rules. That record earns them a top spot on the lists of busy engineering and purchasing teams.
In short, NPN and PNP sensors do the same job but wire up in opposite ways. Picking the right one for your factory line keeps things running smooth, speeds up setup, and cuts unplanned downtime. For B2B firms that depend on robots, packaging machines, or moving parts, making sure sensors match is a must-have step toward dependable equipment.
When you start looking for proximity sensors for your next build or facility refresh, check out Omchele’s complete lineup. With decades on the clock and a global shipping reach, Omchele helps companies get tough, flexible, high-performance sensors fit for today’s automation world.